By Michael
Irving
January 11, 2021
Facebook
Twitter
Flipboard
LinkedIn
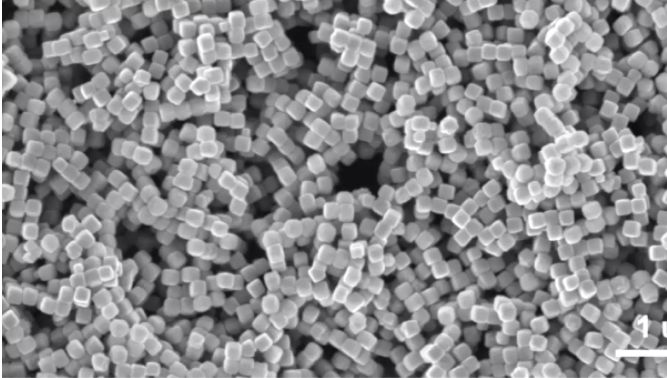
An electron
microscope image of the tiny copper cubes used as a catalyst in the new reactor
Photo credit: Wang Group/ Senftle Group
VIEW 2 IMAGES
Carbon monoxide is often
generated as a byproduct of industrial processes, and while it’s not directly a
greenhouse gas in the atmosphere, it can be an indoor or urban air pollutant
that is harmful to human health in higher concentrations.
In the new study, the Rice
researchers developed a way to turn this potentially dangerous waste product
into something of value. Acetic acid is used in foods such as vinegar, as an
antiseptic, a solvent, and in a range of industrial processes and products.
Building on a previous device the
team used to convert carbon dioxide into formic acid, the new reactor reduces
carbon monoxide into acetic acid.
“We’re upgrading the product from
a one - carbon chemical, the formic acid, to two - carbon, which is more
challenging,” says Haotian Wang, an author of the study. “People traditionally
produce acetic acid in liquid electrolytes, but they still have the issue of low
performance as well as separating the product from the electrolyte.”
In this case the electrolyte is
solid. It interacts with a catalyst made up of nanoscale copper cubes carefully
engineered with corrugated surfaces that help break certain carbon - oxygen
bonds to convert the gas into the desired product.
A diagram of the new reactor that
converts carbon monoxide into acetic acid Peng Zhu
“Sometimes copper will produce
chemicals along two different pathways,” says Wang. “It can reduce CO into
acetic acid and alcohols. We engineered copper cubes dominated by one facet that
can help this carbon - carbon coupling, with edges that direct the carbon -
carbon coupling towards acetic acid instead of other products.”
Deionized water is piped through
the reactor, where it mixes with the acetic acid to produce a usable solution.
The leftover gas is emitted as oxygen.
In lab tests, the device was run
continuously for 150 hours, producing a solution that contained up to two
percent acetic acid – a weak solution, compared even to vinegar’s four percent
acetic acid content, but useful enough. The acid component itself was up to 98
percent pure.
The team says that more work
needs to be done to improve the system in order to make it scalable, including
making it more stable and more energy efficient.
The research was published in the
journal Proceedings
of the National Academy of Sciences.
Source: Rice
University