By Ben
Coxworth
June 03, 2022
Facebook
Twitter
Flipboard
LinkedIn
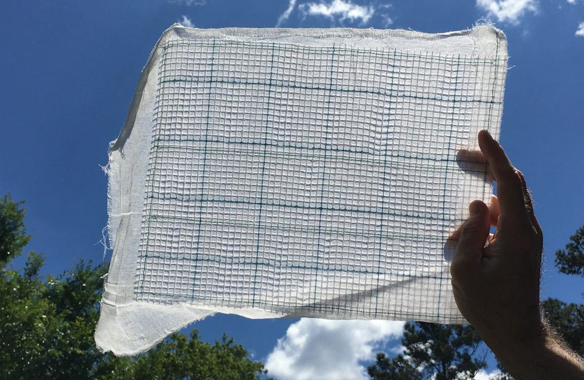
Even after being washed and dried multiple times, the
material remains effective Photo credit: Sonja Salmon
VIEW 1 IMAGES
The current version of the flue gas filter was created by
researchers at North Carolina State University, who started by dunking a
two-layer sheet of cotton in a liquid solution containing a crustacean-derived
material known as chitosan.
The chitosan served as a glue, allowing a naturally
occurring enzyme called carbonic anhydrase to be added as a coating. That
enzyme accelerates a reaction in which CO2 and water combine to form
bicarbonate, which is the main ingredient in baking soda.
The completed filter was twisted into a spiral, which was
then stuffed inside a tube. An air mixture made up of CO2 and nitrogen
(simulating flue gas emissions) was then pumped through that tube, along with a
water-based solution. Reacting with the water and the carbonic anhydrase, much
of the CO2 was converted into liquid bicarbonate that trickled down the filter
and out of the tube, where it was collected.
When the air was pumped through the tube at a rate of 4
liters (1 US gal) per minute, 52.3 percent of the CO2 in that air was harvested
using a single sheet of the filtration material. When two sheets were stacked
and twisted together, that figure rose to 81.7 percent. Even after being washed
and dried five times, the material retained much of its functionality.
That said, the scientists still need to determine how well
a scaled-up version of the technology would work in an actual flue gas chimney,
where gas emission rates can exceed 10 million liters per minute.
A paper on the study, which is being led by postdoctoral
researcher Jialong Shen, was recently published in the journal ACS Sustainable Chemistry & Engineering.
Source: North Carolina State University